What Affects The Plastic Pelletizing Process And How To Optimize?
Plastic extrusion pelletizing is a key step in the conversion of plastic waste into recycled pellets and is related to the quality and value of recycled plastic granules. Therefore, we need to understand the key factors that affect the plastic pelletizing process and optimize them to produce high-quality pellets with less effort.
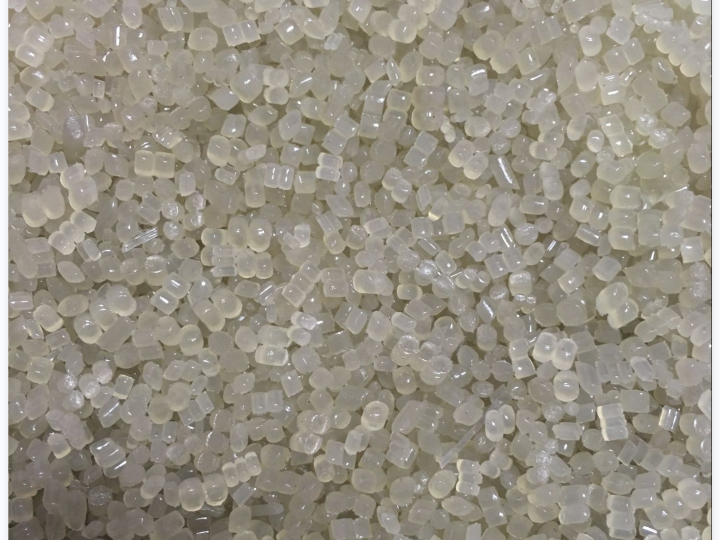
Purity of Recycled Plastic Materials
The higher the purity of the raw material and the better the performance, the lower the impurity content and the better the quality of the plastic pellets after pelletizing. To improve the purity of recycled plastics, we usually wash them first to completely remove grease, dirt, glue and other impurities.
So, how to improve plastic purity? In addition to the collection of high-quality waste plastic, we can choose an effective plastic washing machine, to be pelletized plastic materials for thorough deodorization washing, etc., to improve the quality of plastic recycling.
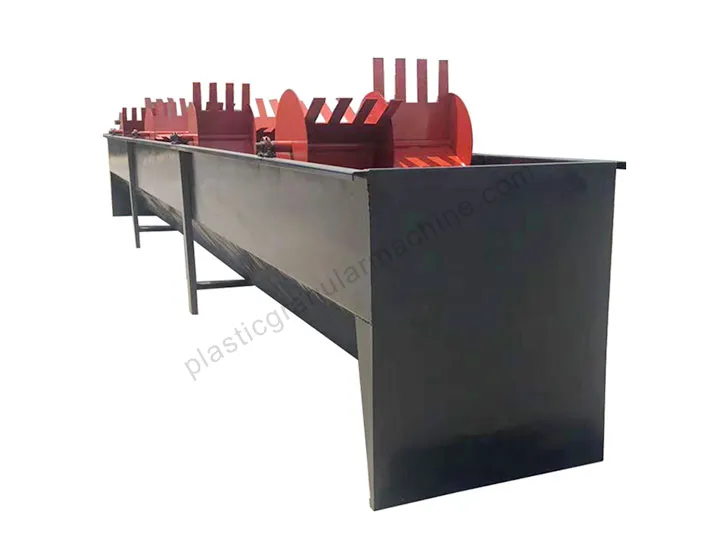
Temperature Control During Plastic Pelletizing Process
Temperature is an important process parameter in the plastic pelletizing process.
Too low a temperature will result in insufficient melting of the plastic, poor melt fluidity, which will affect extrusion molding, resulting in burrs, bubbles and other defects, as well as low production efficiency;
Too high a temperature will destroy the molecular structure of the plastic, reduce performance, produce harmful gases, shorten the life of equipment, and lead to the recovery of particles rough, low quality.
Therefore, it is necessary to set the pelletizing temperature according to the melting point and other characteristics of different plastic materials. It is important to use a high-efficiency plastic extruder machine that can follow the pelletizing process in real-time and control the temperature intelligently.
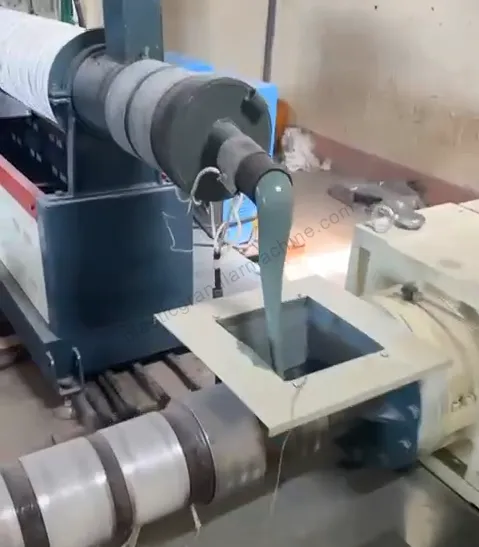
Performance Of The Extrusion Pelletizing Machine
- Proper screw design such as compression ratio, pitch, etc. ensures efficient melting of plastics.
- Stable performance of plastic extruder reduces equipment downtime and improves production efficiency.
- High-capacity die head reduces the number of screen changes and improves pelletizing efficiency.
Follow-up Treatment After Extruding
After the molten plastic is extruded, it needs to be cooled and cut in a timely manner to help stabilize the plastic form and give the pellets a smooth surface and better appearance.
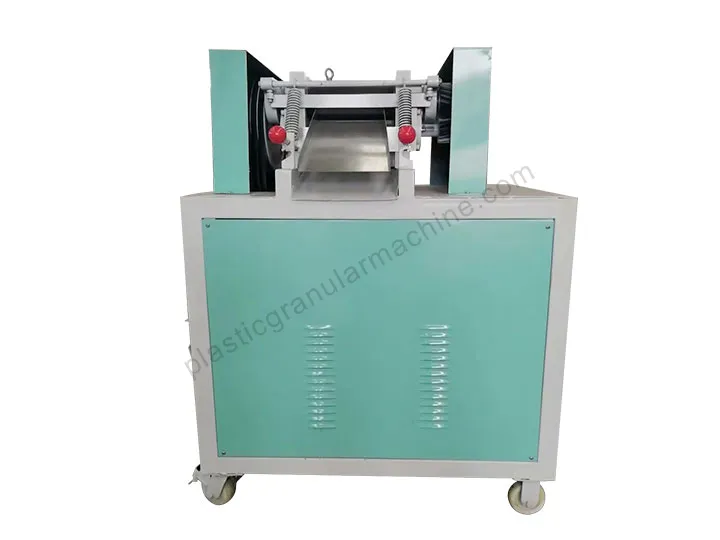
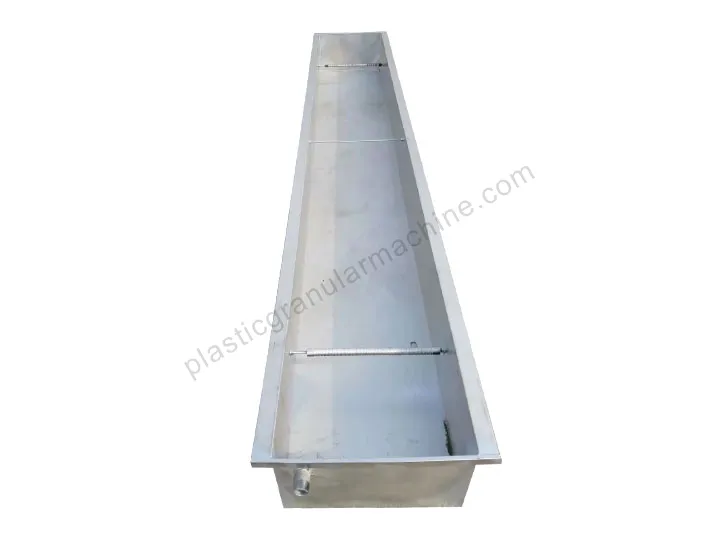
High-quality Plastic Granulation Machine Solving Above Issues
To improve the above mentioned plastic pelletizing influences, in addition to some uncontrollable environmental influences, we can help to achieve high-quality pelletizing through energy efficient machinery.
Efficient’s well-established plastic pelletizing systems are widely used all over the world to improve the quality of plastic pellets and increase the pelletizing efficiency:
- Plastic washing machine with low energy consumption, high efficiency, saving water and at the same time can realize the thorough washing of plastic;
- Plastic extruder adopts advanced screw melting technology and is equipped with drawbar die head and water ring cutting die head for choice;
- Equipped with intelligent cabinets for easy operation and control of plastic pelletizing temperature;
- We also provide complete after-sales service, giving you the promise of quality assurance.
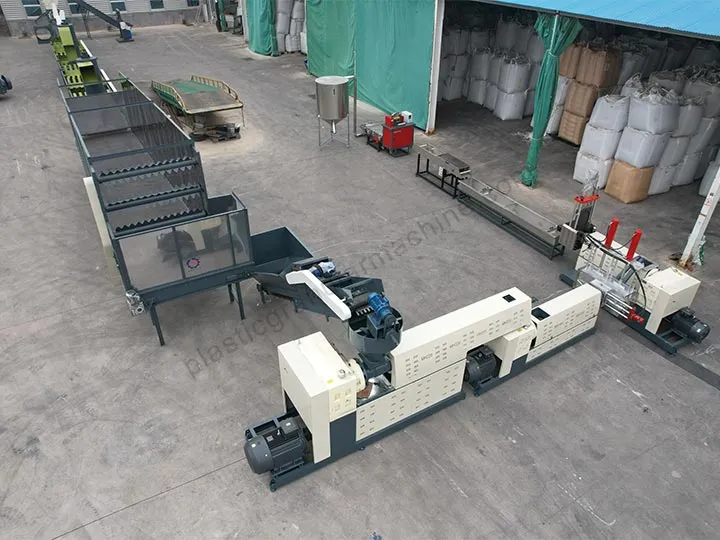
Summary
In summary, the influence of plastic pelletizing factors include raw material purity, pelletizing temperature, plastic extruder performance and so on. If you are struggling with plastic pelletizing, please feel free to contact us, we will provide you with the perfect plastic pelletizing solution!